Expert Guidance on What is Porosity in Welding and How to Address It
The Scientific Research Behind Porosity: A Comprehensive Overview for Welders and Fabricators
Understanding the detailed mechanisms behind porosity in welding is vital for welders and fabricators aiming for impressive workmanship. As metalworkers delve right into the depths of this phenomenon, they reveal a globe regulated by numerous elements that influence the development of these small spaces within welds. From the structure of the base products to the details of the welding process itself, a multitude of variables conspire to either aggravate or reduce the visibility of porosity. In this thorough guide, we will certainly unravel the scientific research behind porosity, exploring its effects on weld high quality and unveiling advanced methods for its control. Join us on this journey via the microcosm of welding imperfections, where accuracy fulfills understanding in the pursuit of perfect welds.
Comprehending Porosity in Welding
FIRST SENTENCE:
Examination of porosity in welding exposes essential insights right into the integrity and high quality of the weld joint. Porosity, identified by the visibility of dental caries or voids within the weld metal, is an usual concern in welding procedures. These spaces, otherwise correctly resolved, can jeopardize the architectural honesty and mechanical residential properties of the weld, causing possible failures in the finished item.
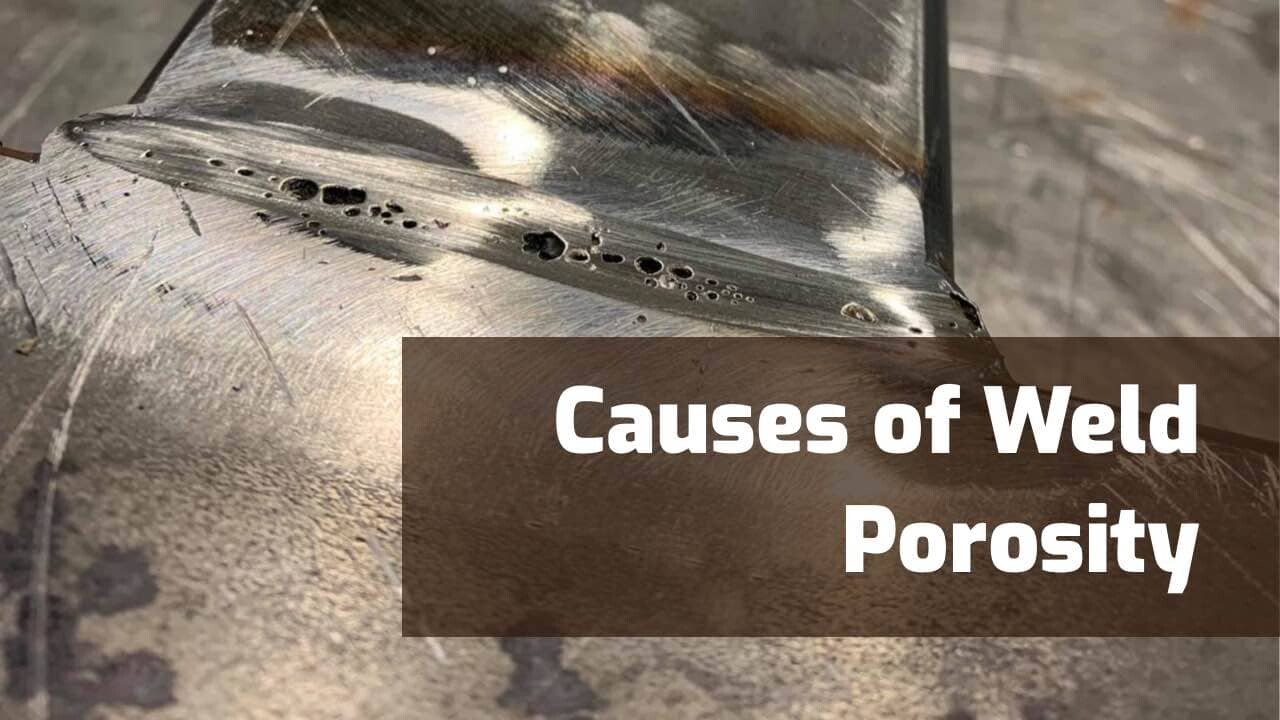
To discover and measure porosity, non-destructive testing techniques such as ultrasonic testing or X-ray evaluation are typically used. These techniques permit the identification of inner flaws without jeopardizing the stability of the weld. By evaluating the dimension, shape, and circulation of porosity within a weld, welders can make enlightened choices to boost their welding procedures and attain sounder weld joints.

Aspects Affecting Porosity Development
The event of porosity in welding is influenced by a myriad of aspects, ranging from gas securing effectiveness to the complexities of welding specification settings. Welding parameters, consisting of voltage, current, take a trip rate, and electrode kind, also impact porosity formation. The welding strategy used, such as gas metal arc welding (GMAW) or protected steel arc welding (SMAW), can affect porosity development due to variations in warm circulation and gas protection - What is Porosity.
Results of Porosity on Weld Quality
Porosity development dramatically compromises the architectural honesty and mechanical residential properties of welded joints. When porosity is present in a weld, it produces spaces or cavities within the product, reducing the general strength of the joint. These voids function as tension concentration factors, making the weld extra susceptible to cracking and failing under load. The existence of porosity additionally compromises the weld's resistance to corrosion, as the trapped air or gases within deep spaces can react with the surrounding environment, bring about degradation with time. Additionally, porosity can hinder the weld's ability to endure pressure or impact, additional threatening the general quality and dependability of the welded structure. In important applications such as aerospace, auto, or architectural building and constructions, where safety and security and resilience are paramount, the damaging effects of porosity on weld quality can have severe repercussions, highlighting the significance of decreasing porosity with proper welding techniques and procedures.
Techniques to Decrease Porosity
To improve the top quality of bonded joints and make sure architectural stability, welders and fabricators use advice particular strategies aimed at lowering the formation of spaces and dental caries within the product during the welding process. One reliable approach to reduce porosity is to ensure proper product preparation. This consists of comprehensive cleansing of the base metal to remove any type of impurities such as oil, grease, or wetness that can add to porosity development. Additionally, making use of the appropriate welding specifications, such as the proper why not try these out voltage, current, and take a trip rate, is essential in protecting against porosity. Keeping a regular arc length and angle during welding likewise aids reduce the possibility of porosity.

Moreover, picking the right securing gas and keeping correct gas circulation rates are essential in lessening porosity. Making use of the suitable welding method, such as back-stepping or employing a weaving activity, can additionally aid disperse warmth equally and lower the possibilities of porosity development. Guaranteeing correct ventilation in the welding setting to eliminate any prospective resources of contamination is vital for achieving porosity-free welds. By carrying out these techniques, welders can successfully reduce porosity and create top notch bonded joints.
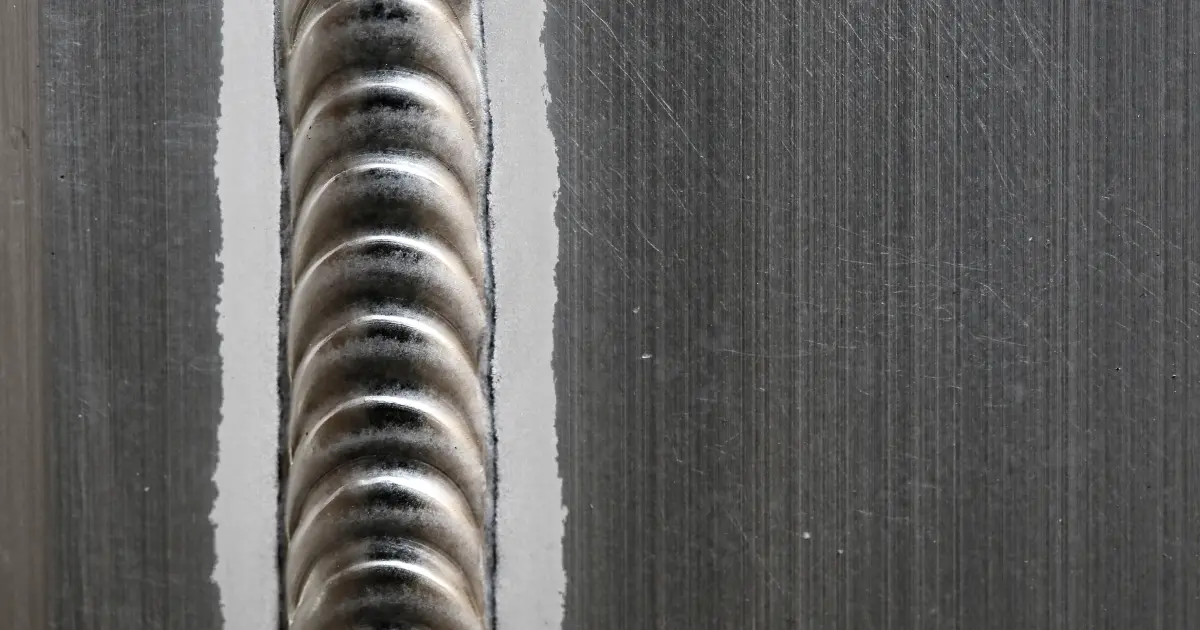
Advanced Solutions for Porosity Control
Carrying out innovative technologies and cutting-edge approaches plays a critical function in achieving remarkable control over porosity in welding procedures. Additionally, utilizing advanced welding methods such as pulsed MIG welding or changed atmosphere welding can likewise aid mitigate porosity concerns.
An additional innovative solution entails the usage of sophisticated welding tools. For example, utilizing devices with integrated functions like waveform control and advanced source of power can improve weld high quality and lower porosity dangers. In addition, the application special info of automated welding systems with specific control over criteria can significantly minimize porosity defects.
Furthermore, integrating advanced monitoring and inspection technologies such as real-time X-ray imaging or automated ultrasonic screening can assist in identifying porosity early in the welding process, permitting prompt rehabilitative actions. Generally, incorporating these innovative remedies can significantly boost porosity control and enhance the overall top quality of bonded elements.
Conclusion
In verdict, comprehending the science behind porosity in welding is essential for welders and makers to produce top quality welds - What is Porosity. Advanced services for porosity control can better improve the welding procedure and make sure a strong and reliable weld.